Research
The research concerns advanced turbomachinery, thermo-mechanical energy storage, efficient heat transfer and sustainable heat-to-power conversion technologies. Relevant applications include geothermal energy, concentrating solar power, electric vehicles, and waste heat recovery in the maritime and heavy-duty transport sectors and industry.
Advanced turbomachinery
Turbomachinery with two-phase flow represents the backbone of several emerging clean technologies, including, for example, partial evaporation organic Rankine cycle systems (PEORC), supercritical carbon dioxide (sCO2) Brayton cycle systems, liquid air energy storage (LAES) systems employing a two-phase expander for the air liquefaction process, and trans-critical carbon dioxide heat pumps. The design and operation of turbomachinery with two-phase flow is highly challenging because of the presence of droplets/bubbles in the flow tends to deteriorate the efficiency of the machinery and cause erosion on the blading, which may cause structural damage and/or vibrations, thus affecting the performance and reliability of such devices. In addition, the design of turbomachinery with two-phase flow calls for the need of advanced numerical models, which are currently not available. In the context two-phase turbomachinery, we develop advanced non-equilibrium models for different applications. The models are used to identify the loss mechanisms and quantify the loss penalty deriving from the presence of the droplets/bubbles in the flow. Based on the results, optimal blading designs for two-phase turbomachinery are derived. Advanced high-fidelity computational fluid dynamics (CFD) models as well as mean-line approaches are adapted.
Thermo-mechanical energy storage
Large-scale energy storage systems are promising options to mitigate the variability of renewable energy sources and to balance the energy supply and demand. Pumped thermal energy storage (PTES) holds promise as a long-duration energy storage technology due to its independence of geographical constraints and critical materials. Compared to other thermo-mechanical energy storage technologies, PTES has low maturity but is rapidly evolving. Liquid air energy storage (LAES) is another novel technology that has recently gained increasing attention. The LAES system is not geographically restricted and requires much less storage volume than those of the more mature technologies – in the order of 700 times less than that of compressed air energy storage. The LAES system comprises three processes (see the figure): 1) charging process – excess electricity (e.g. from wind and/or solar energy) is used to drive a liquefaction process, 2) storing process – liquid air is stored in cryogenic tanks at nearly ambient pressure, and 3) discharging process – the liquid air is pressurized, regasified and expanded in turbines producing electricity. At present, the LAES technology is at an industrial demonstration level.
Efficient heat transfer
For environmental reasons, currently a paradigm shift is taking place in terms of working fluids/refrigerants in power cycles/refrigeration systems. New working fluids are being introduced for which there are no data on their performances in different heat transfer devices available in the open literature, urgently calling for the need of research. We investigate and identify the governing heat transfer mechanisms of pure fluids as well as zeotropic mixtures in plate heat exchangers using both experimental and numerical analysis. Based on the results we develop novel prediction methods for the thermal-hydraulic performance of flow boiling/condensation.
Large parts of the world are currently transitioning towards the use electric vehicles, calling for research supporting the development and implementation of electric vehicles. In this context we perform innovative thermal analyses of on-board energy management systems coupling the HVAC system, battery pack, electric motor and, in some cases, on-board chargers. Furthermore, optimal control strategies for the novel integrated on-board energy management systems are developed. The overall goals of the analyses are to make the electric vehicles more efficient and to minimize the degradation of the batteries due to their cyclic operation.
Molten salt-gas cooled heat exchangers are used in concentrating solar power plants, pumped thermal energy systems and process industries. The cyclic operation of molten salt heat exchangers rises concern regarding the potential freezing of salts due to their high freezing temperature. Therefore, pinpointing the initiation of salt solidification and forecasting the phase change behavior in high-temperature heat exchange processes is necessary, as these factors influence the design and operation of the heat exchangers. We conduct first-of-its-kind multi-dimensional, transient computational fluid dynamics analysis aiming at replicating the conditions the molten salt experiences during operation in a concentrating solar power plant or pumped thermal energy systems.
Sustainable heat-to-power conversion technologies
In order to evaluate the technical and economic feasibility of sustainable energy conversion concepts, it is necessary to make a techno-economic analysis, considering the performance of the system as well as economic indicators. We perform techno-economic analyses to evaluate the prospects for novel energy storage systems, including organic Rankine cycle (ORC) systems using pure fluids as well as mixtures, supercritical carbon dioxide (sCO2) Brayton cycle systems, and solar collector systems for concentrating solar power (CSP) applications. We consider both design and off-design operation and, when relevant, incorporate dynamic models in the design and analysis of power systems. Recognizing that the design problem is a complex task governed by numerous parameters and constraints, we employ state-of-the-art optimization techniques to maximize the performance of these systems while effectively balancing multiple criteria. By leveraging accurate numerical models and optimization strategies, we strive to advance energy conversion solutions that are efficient, cost-effective, and sustainable.
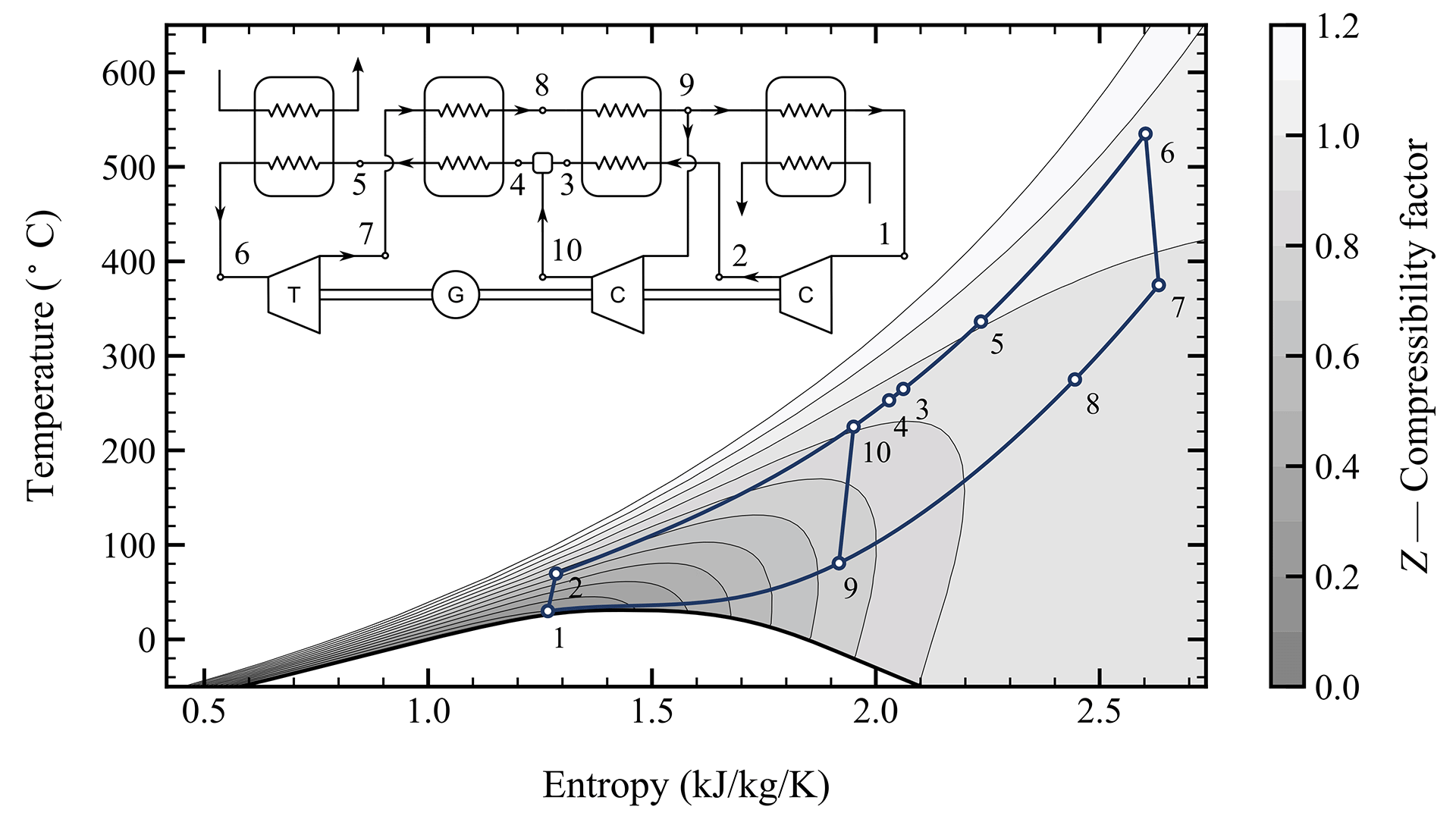